CAPITULO 4 Kanban
4.1 Introducción
Es un sistema de scheduleo para lean manunfactoring y Just in time manufacturing (JIT). Taiichi Ohno desarrollo kanban para mejorar la eficiencia manufacturera y se vuelve un método para alcanzar JIT. Uno de los principales beneficios de kanban es establecer un limite superior a Work in Progress (WiP) inventario para evitar sobrecapacidad. Existen otros sistemas como CONWIP. La meta de Kanban desde este punto de vista es limitar el exceso de inventario a cualquier punto de producción.
4.1.1 Etimología y Origen
La etimología (del japonés) tarjeta o señal y (del chino) señal o tablero. Está diseñado por David J. Anderson para la gestión del flujo de trabajo, basado en los sistemas Lean Manunfacturing a los que dio pie el trabajo de Toyota.
Basado en sistema Just in Time que representa un sistema de arrastre. Es decir, la producción se basa en la demanda de los clientes
Se evita la Práctica push de fabricar productos e intentar venderlos.
4.2 Toyota Production System (TPS)
4.2.1 Intro
Es un sistema socio-técnico que se desarrollo en Toyota que comprende una filosofía de gerencia y de prácticas. Es un sistema de gerencia que organiza manufactura y logistica para automotriz, incluyendo interacción con proveedores y consumidores. Es un precursor del más genérico lean manufacturing de Taiichi Ohno y Eiji Toyoda. Originalmente fue llamado Just in Time production. Los principios que sostienen el TPS están englobados en The Toyota Way
4.2.2 The Toyota Way
Consiste en dos áeas: Mejora continua y Respeto por las personas. En total engloba 14 principios divididos en 4 secciones:
- Filosofía a Largo Plazo
- El proceso correcto producirá los resultados correctos
- Añadir valor a la organización desarrollando a tus personas
- Continuamente resolver problemas de raiz lleva a un aprendizaje organizacional
4.2.3 Toyota Production System House
Visualmente la podemos esquematizar como una casa compuesta de o la Toyota Production System House que se compone de la meta, los pilares, las bases y los cimientos:
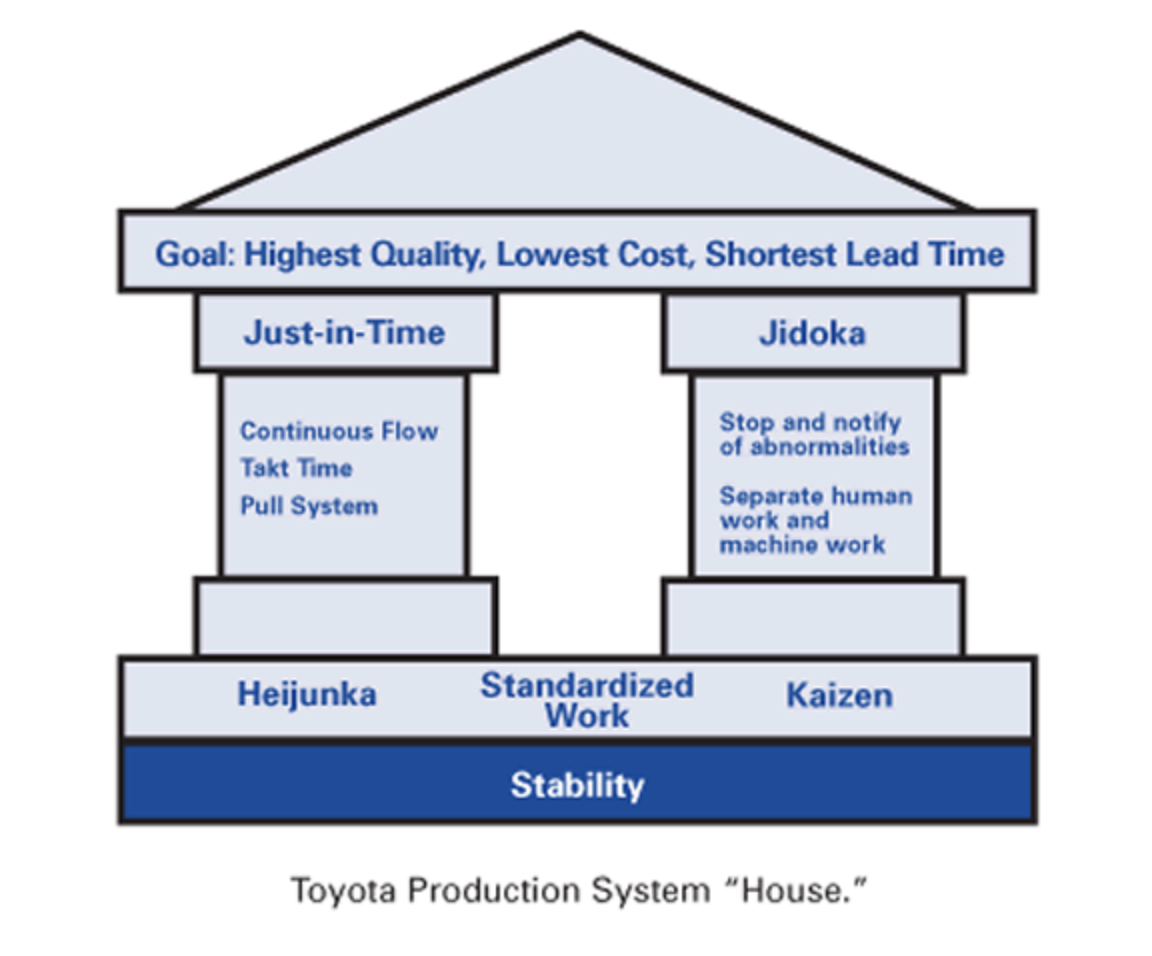
- Meta: La mejor calidad, el menor costo y corto tiempo de entrega.
- Pilares:
Just-In-Time (Justo a tiempo): Producir sólo lo necesario, en el momento justo, en la cantidad necesaria, con lo mínimo necesario.
Continuous flow
Takt Time
Pull System
Built-in Quality (Construir con calidad): Comenzar desde el inicio a construir con calidad, prevenir que si se presentan defectos pasen al siguiente proceso, asegurando así la calidad durante el proceso de producción
Stop & Notify of abnormalities
Separate Man, Machine Work
- Bases: - Standarized Work
Level production
Kaizen: Significa “cambio para mejorar”; deriva de las palabras KAI-cambio y ZEN-bueno. Kaizen es el cambio en la actitud de las personas. Es la actitud hacia la mejora, hacia la utilización de las capacidades de todo el personal, la que hace avanzar el sistema hasta llevarlo al éxito.
- Cimientos:
VSM (Value-Stream mapping). Es parte del Lean-Management Method para analizar el estado actual y diseñar un estado futuro para los eventos que llevan a un producto al cliente final. Es una herramienta visual que muestra todos los pasos críticos en un proceso específico y cuantifica facilmente el tiempo y volumen tomado en cada etapa.
ID Waste: Proviene del Lean Six Sigma (8 wastes). Identificar los tipos de desperdicio, sobreproducción, tiempos de espera, transporte, sobreprocesamiento, inventarios innecesarios, movimientos innecesarios, defectos y talento humano.
Visual Mgmt: Visual Management, para tener el conocimiento, el objetivo de la empresa. Conocer desde arriba hasta abajo.
5S & Safety. Los primeros 5 pilares provienen de Lean Workplace, y el sexto se añade:
Sort: Organización. Mantener solo lo que es necesario y descartar todo lo demás. Si en duda, descartarlo.
Set in Order: Orden, arreglando y etiquetando solo los productos necesarios para su facil uso y encontrarlos facilmente.
Shine: Limpieza. Mantenar todo limpio para inspección. Para seguridad y mantenimiento preventivo.
Standarize: Limpieza estandarizada. El estado que existe cuando los primeros tres pilares “S” son propiamente mantenidas.
Sustain: Sostener la disciplina. Hacer el hábito de mantener propiamente los procedimientos.
Safety:
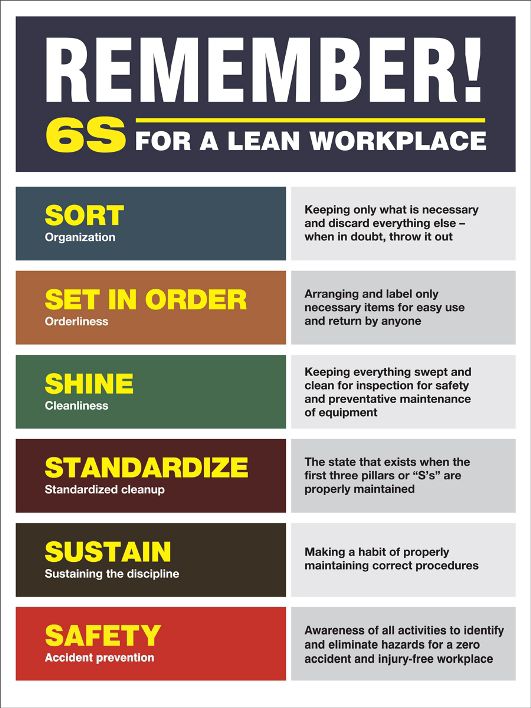
4.3 Las 3 M’s
También se les conocen como las 3M de Toyota. Los conceptos no pueden ser vistos por separado, ya que en conjunto, presentan las barreras para el valor. El oibjetivo debe ser identificar y eliminar las 3M en las disitintas etapas del proceso a mejorar. El Muda es comunmente el que se enfoca a eliminar por que es más fácil de encontrar, pero el Mura y Muri son muchas veces causas raíz del Muda, producto de irregularidades y tensiones existentes.
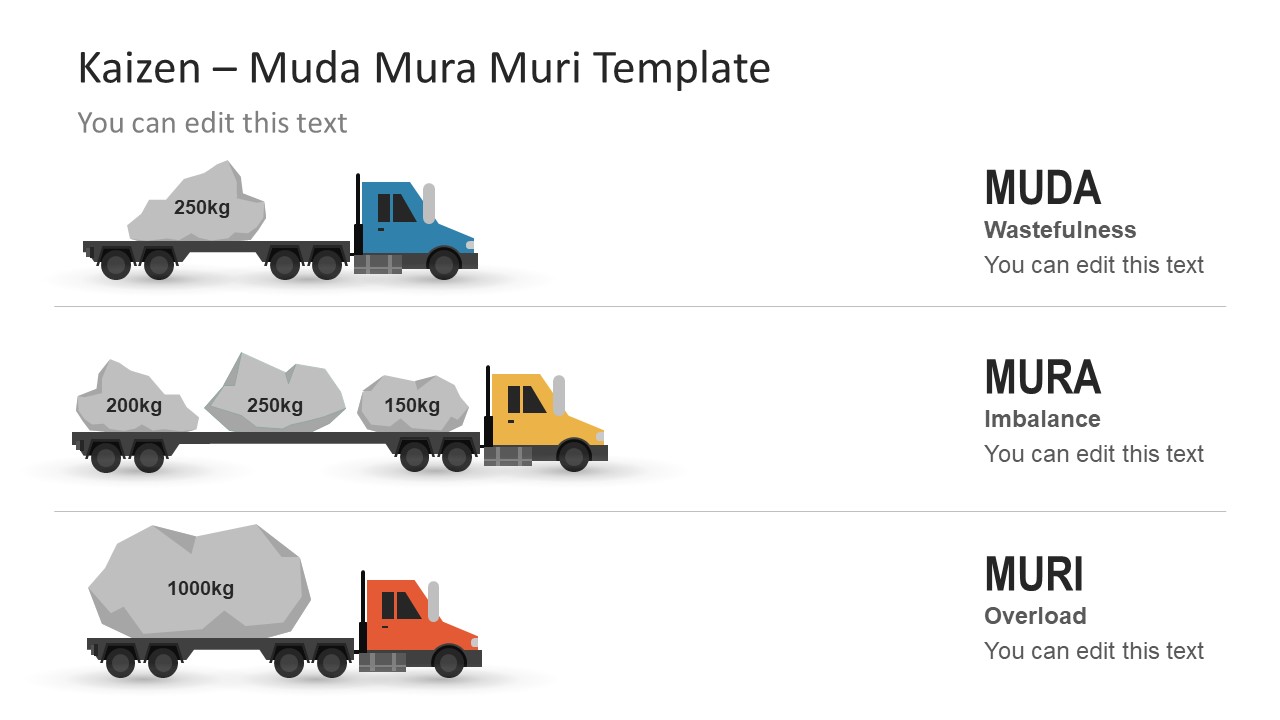
4.3.1 MUDA
- MUDA: Evitar procesos que consumen recursos y no agregan valor extra al producto/cliente. Las 8 categorías para reducir el Muda se relacionan son (8 wastes):
Defects: Esfuerzo extra causado por falta de definión, información incorrecta, esfuerzos causados por retrabajo, chatarra, información incorrecta.
Overproduction: Produccion que es más quer necesaria o antes que sea necesitada
Waiting: Tiempo desperdiciado para los sigueintes pasos en un proceso
Non-Utilized Talent: Talento, skills o conocimiento subutilizado
Transportation: Traslados no necesarios de productos y materiales
Inventory: Exceso en productos y materiales que no se procesaron
Motion: Movimientos no necesario de personas
Extra-processing: Más trabajo o más calidad de la requerida por el cliente
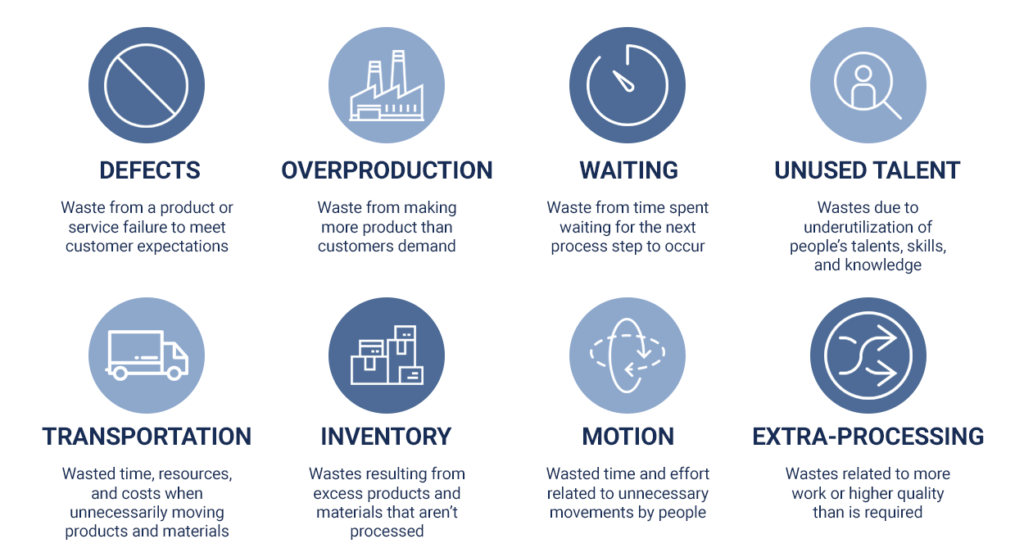
4.4 Kanban
Es un método para definir, gestionar y mejorar servicios que entregan valor, tales como servicios profesionales, trabajos o actividades qne las que interviene la creatividad y el diseño tanto de productos de software como físicos.
Se caracteriza por el principio de “empieza por donde estés,” por medio del cual se consigue catalizar el cambio rápido y focalizado, reduce la resistencia y ayuda a trabajar en línea con los objetivos de la organización.
El método Kanban se basa en hacer visible lo que es trabajo intangible, para asegurar que el trabajo es requerido y necesitado por el cliente, el equipo tiene la capacidad de entregar.
4.4.1 9 Valores Kanban:
- Transparencia: Un intercambio abierto de información y un vocabulario claro y no ambiguo que permita crear transparencia en otras las areas.
- Equilibrio: Se es eficiente para balancear los diferentes requerimientos, vistas y habilidades de todos los participantes entre ellos.
- Colaboración: El método Kanban mejora la manera en que las personas trabajan juntas. Colaboración es uno de los puntos principales.
- Foco en el cliente: Los clientes y el valor que se les brinda son el centro de interés de todas las personas involucradas en la compañía.
- Flujo: El trabajo representa a un flujo continuo u ocasional de cadena de valor. Un punto de inicio para usarlo en Kanban es reconocer y mantener ese flujo.
- Liderazgo: El liderazgo es requerido a todos los niveles para generar valor y mejorar el estado actual.
- Entendimiento: Implica el self-awareness individual y de la organización para movernos hacia adelante. Kanban es un método de mejora que requiere cambio, que requiere entendimiento. Una vez que se identificó un problema, se determina causa y efecto. Esto significa que se necesita ententer el trabajo y el proceso involucrado para poder mejorarlo. Empieza con lo que haces y entiende como lo estas haciendo.
- Acuerdo: En un acuerdo todas las partidos acuerdan perseguir las mismas metas juntos. Diferentes opiniones y visiones deben ser respetadas. Todas estos diferentes puntos de vista deben converger eventualmente. Este parte de el compromiso de las personas involucradas en el proceso para en conjunto mejorar el cumplimiento de los objetivos.
- Respeto: Respeto por las personas en la forma de aprecio del trabajom, entendimiento y consideración es funcamental. Empezar con lo que haces y despues mirar si se cumple o no cumple en objetivo o necesidades dentro de la organización.
4.4.2 3 Principios directores Kanban:
- Sostenibilidad (Hacia adentro):
- Orientación al servicio (Hacia afuera):
- Supervivencia (Hacia el futuro):
4.4.3 6 Principios fundacionales Kanban:
Se pueden dividir en tres principios de gestión del cambio (GC) y tres principios de prestación de servicios (PS):
- (GC) Comienza con lo que haces ahora entendiento los procesos actuales, respetando roles existentes
- (GC) Acuerda buscar la mejora a través del cambio evolutivo
- (GC) Fomenta actos de liderazgo a todos los niveles, desde contribuyentes a directivos
- (PS) Comprendere y concentrarse en necesidades y expectativas de clientes
- (PS) Administra el trabajo, que la gente se auto-organice
- (PS) Organización es un ecosistema de servicios independientes, guiados por políticas
4.4.4 Prácticas Kanban
Visualizar: Representa un sistema de flujo en el que los elementos de trabajo fluyen a través de las distintas etapas de un proceso.
Limitar el WiP: Se consigue con la implementación de sistemas pull en los que el enfoque principal es la generación de unidades terminadas y no la acumulación de unidades en progreso.
Gestión del flujo de trabajo: Una de las claves para maximizar el flujo de valor es conocer el coste de retraso de los elementos de trabajo. Esto es, la cantidad de valor del elemento que se pierde debido al retraso de la implementación durante un periodo de tiempo.
Hacer explicitas las políticas: Las políticas del proceso deben ser escasas, simples, estar bien definidas, visibles, deben aplicarse siempre y tienen que ser facilmente modificables por los que proporcionan el servicio
Circuitos de retroalimentación: ### Herramientas Kanban:
4.5 Kanban board
Kanban board se puede dividir en 5 componentes: Señales Visuales, Columnas, Work-in-progress limites, puntos de compromiso, y punto de entrega.
- Visual Signals: Las personas del equipo escriben proyectos y items de trabajo en tarjetas, usualmente una por tarjeta. Para equipos agiles, cada tarjeta puede encapsularse en una historia de usuario.
- Columnas: Se representan una actividad en especifico que juntas componen el “Workflow.” El flujo de tarjetas hasta que se complete. Puede ser: To Do, In progress, Complete o mucho más completa.
- WiPs limites: Son el máximo numero de tarjetas que pueden haber en una columna. Cuando la columna se llena, el equipo necesita en conjunto moverlas antes que nuevas cartas entren al workflow. Es importante para exponer los cuellos de botella en el workflow y maximizar el flujo.
-Punto de compromiso: Los equipos de Kanban frecuentemente tienen un backlog del tablero. Esto es cuando los clientes y participantes del equipo ponen sus ideas para proyectos que el equipo puede tomar cuando se inicia el proyecto
-Punto de entrega: El punto